What if there was a way to simplify the intricate process of design optimization? What if we could predict and refine the performance of designs before they're physically created? Indeed, this is achievable through Finite Element Analysis (FEA). This advanced computational tool is reshaping the engineering landscape by providing the opportunity to simulate, analyze, and enhance designs within a virtual environment. This discourse delves into the critical aspects of FEA, highlighting its pivotal role in refining models. It represents a scenario where cutting-edge technology and creativity join forces to achieve engineering excellence.
Profound Insight into Finite Element Analysis
Finite element analysis is a sophisticated numerical method for resolving complex engineering problems. It involves breaking down an object into numerous small, straightforward sections known as 'finite elements.' Each of these elements is examined independently, with their cumulative behavior providing an accurate representation of the entire object. This process can be likened to a detailed jigsaw puzzle, where each piece signifies a portion of the larger structure. Achieving an optimal finite element analysis model is essential for precise simulation.
Each element corresponds to fundamental components of design physics, whether it's forces, materials, or constraints. The cooperative behavior of these minute elements, stacked like bricks in a structure, culminates in a robust and harmonious final design. This effectively encapsulates the essence of FEA, which is understanding the whole by localizing the complexity. Consider these elements as individual threads, each contributing to the strength of a tightly woven fabric, which signifies a comprehensive design.
Analyzing each 'finite element' enables precise insights into potential stress points, deformations, or weaknesses, thus empowering engineers with actionable data. FEA functions as a strong safeguard measure, fostering the progression of ambitious design initiatives and deciphering complex challenges amidst a period of heightened engineering complexity. The versatility of FEA, applicable across various domains such as thermal, structural, or even electromagnetic, further underscores its significance in design engineering. This unique combination of mathematical strictness and engineering insight that FEA brings to the table confirms its importance in the domain of improving theoretical frameworks.
Importance of Finite Element Analysis in Improving Designs
Finite element analysis is an indispensable computational tool in engineering, crucial for enhancing the quality of designs. Its integration into FEA optimization processes is essential for accurately assessing and predicting design performance under diverse scenarios.
-
Design Integrity Assessment
FEA is a critical tool for verifying the structural integrity of a design. It provides engineers with the ability to validate the durability and toughness of their designs under a multitude of realistic conditions. By simulating various physical phenomena, including force impacts and thermal stress, FEA negates the requirement for multiple physical prototypes, enhancing the overall effectiveness of the model refinement process.
-
Proactive Predictive Analysis
Leveraging FEA simulation services enables a proactive design approach through predictive analysis. These specialized finite element services equip engineers with the capacity to anticipate and troubleshoot potential design challenges before they manifest. FEA's ability to predict a design's performance under future operational conditions negates the need for reactive modifications, fostering a solution-oriented methodology.
-
Achieving Cost Optimization
FEA is instrumental in achieving economic value in model refinement. It significantly reduces expenses associated with physical prototyping and experimental testing. More importantly, FEA's ability to detect design flaws at an early stage in the development process mitigates the financial implications of product failures later on.
-
Design Sophistication
FEA is a powerful tool when it comes to managing design complexity. By segmenting complex physical phenomena into finite elements, FEA elucidates these entities, making them more accessible for scrutiny and understanding. FEA equips engineers with the capacity to explore sophisticated designs, enabling the prediction of their behavior with enhanced accuracy.
-
Streamlining Material Selection
FEA aids engineers in refining the process of material selection for their designs. It simulates the behaviors of different materials under various operational conditions, facilitating the determination of the most suitable and cost-effective materials for specific design applications.
-
Performance Validation
FEA operates as a strong system for ensuring design performance. It provides an exhaustive understanding of how a design will perform under different scenarios and operating conditions, ensuring adherence to the stipulated standards and specifications.
-
Iterative Process Acceleration
FEA contributes to the acceleration of the iterative design process by providing instantaneous feedback on design modifications. This allows engineers to swiftly evaluate the impacts of alterations, expediting the iterative process and leading to an optimized design in a short time frame.
-
Risk Mitigation
FEA effectively mitigates design risks by enabling engineers to identify and rectify potential design issues at an early stage of the development cycle. This proactive approach minimizes the likelihood of product failure and associated liabilities, ensuring design safety and reliability.
-
Comprehensive Analysis
FEA offers an in-depth design analysis by modeling complex geometries, materials, and boundary conditions. It delivers a nuanced understanding of design performance, fostering data-driven decision-making and the achievement of high-quality designs.
FEA Techniques: Essential for Advancing Designs
The quest for superior designs is a crucial aspect of engineering projects, with finite element analysis serving as a vital strategy for navigating this complexity. FEA, a computer-aided engineering discipline, enables the simulation of product interactions with various forces, thermal effects, vibrations, and other physical phenomena. This document provides an in-depth exploration of three specific FEA methods crucial for enhancing designs.
-
Optimal Material Arrangement
Topology optimization is an advanced mathematical model that strategically manipulates material distribution within a predefined design space. This method provides a systematic approach to minimize material usage, concurrently maintaining the structural integrity of the design. It proves particularly beneficial in complex load cases and boundary conditions catalyzing the development of innovative and resource-efficient designs.
-
Geometry Refinement
Shape optimization, a vital aspect of FEA, fine-tunes the geometric attributes of a design to improve its performance. By modifying a structure's shape under specific constraints, it enhances the design's functionality. This process significantly mitigates stress concentration, strengthens load-bearing capacity, and enhances overall design performance - all contributing to a more efficient and sturdy final product.
-
Dimensional Modification
Sizing optimization zeroes in on adjusting the dimensions of design components to optimize performance. This process involves varying size parameters such as the thickness of a plate or the cross-sectional dimensions of a beam, under specific load and boundary conditions. Particularly effective in limited design spaces, it seeks to attain maximum performance using minimal material, thereby reducing weight, enhancing stiffness, and boosting overall design efficiency.
Traversing the FEA Roadmap - Precise Steps for Improving Designs
Finite element analysis employs a meticulous and detailed methodology tailored for enhancing the quality of designs in engineering services. By using finite element analysis (FEA) services, every design detail is meticulously analyzed and optimized to ensure optimal performance. This analytical process ensures exactness in the implementation of design optimization strategies.
-
Model Reduction
The initial phase in FEA involves the simplification of complex designs into essential elements. The primary focus is to strip away non-critical details and emphasize the key design components that significantly influence performance. This step enables the FEA process to be more manageable and efficient, setting the stage for a deep analysis of structural, thermal, and mechanical attributes of the design.
-
Boundary Conditions Specification
Accurate simulations depend on the precise definition of boundary conditions, which include the constraints and forces the model will face in its working environment. The procedure involves applying loads, supports, and environmental conditions that accurately mirror actual operating scenarios. Establishing these parameters ensures the subsequent analysis faithfully reproduces the dynamics of these scenarios, yielding trustworthy and pertinent findings.
-
Finite Element Discretization
The core of FEA involves dividing the design space into distinct 'finite elements.' This mesh creation process converts the simplified model into a large network of manageable units. The fundamental laws of physics are applied within these units, enabling a detailed analysis that captures the complex interaction of stresses and strains across the model.
-
Mesh Refinement
Once the initial mesh is created, the focus shifts to refinement, particularly in areas anticipated to bear significant stress concentrations. This refinement process enhances the analysis's accuracy by increasing the element density in crucial areas, thereby capturing detailed behaviors under imposed loads or constraints. This detailed insight is vital for identifying potential weak spots or failure points within the design.
-
Results Interpretation
The culmination of the preceding stages leads to the interpretation phase, where the computed data is rigorously analyzed to comprehend the design's behavior under simulated conditions. Engineers examine the results for insights into stress distributions, deformation patterns, and potential failure modes. This critical phase determines whether the design meets the performance criteria or requires further refinement.
-
Achieve Optimization
The final stage in the FEA process is optimization, where the analysis results inform iterative improvements to the design. These enhancements could involve material changes, geometric modifications, or a reassessment of the applied loads and boundary conditions. The objective is to refine the design iteratively until it achieves an optimal balance of performance, reliability, and cost-effectiveness, marking the pinnacle of engineering effectiveness.
The Impact of FEA on Industries
Finite element analysis is a flexible digital tool that has dramatically transformed various industries. By simulating physical phenomena, FEA enables engineers to optimize designs and solve complex issues, thereby significantly improving productivity. Here, we explore a few key sectors that have been revolutionized by this advanced technology.
-
Aerospace Industry
The aerospace industry is one where safety and accuracy are paramount. By leveraging FEA, aerospace engineers can evaluate the structural integrity of aircraft components under various stress conditions. This predictive power can lead to safer, more efficient designs and ultimately enhance the airworthiness of aircraft.
-
Automotive Industry
In the automotive industry, FEA has become indispensable in designing and optimizing vehicles. It allows engineers to create virtual prototypes, test them under various conditions, and predict their behavior on the road. This reduces the need for expensive physical prototypes, accelerates the design process, and helps meet stringent safety standards.
-
Civil Engineering
FEA has had a profound impact on civil engineering, particularly in structural analysis. It aids in the design of complex structures such as bridges, tunnels, and skyscrapers, ensuring they can withstand various load conditions. This results in safer and more robust structures, which ultimately benefits society.
-
Medical Industry
In the medical field, FEA is used to understand complex biological systems and develop medical devices. For example, it can simulate the interaction between a device and human tissue, providing valuable insights for improving design quality. This can lead to the development of more effective and safer medical devices.
-
Energy Industry
FEA is also revolutionizing the energy sector, particularly in the design and analysis of equipment used in power plants and renewable energy systems. It enables engineers to assess the performance of components under extreme temperature and pressure conditions, leading to increased effectiveness and safety.
-
Electronics Industry
In the electronics industry, FEA is used to predict and manage the thermal and structural behavior of electronic components. This enables manufacturers to ensure the reliability and longevity of their products, giving them a competitive edge in the market.
Key Benefits of Finite Element Analysis for Businesses
As businesses in the engineering and manufacturing sectors continually strive for effectiveness and precision, finite element analysis has emerged as an indispensable tool. FEA is a computer-aided engineering (CAE) technique that uses a numerical method to predict how a product or material will respond to forces in actual conditions. Here, we delve into the benefits of FEA that make it a vital asset for B2B operations.
-
Optimizing Product Lifecycle
FEA plays a crucial role in the product lifecycle management (PLM), enabling exhaustive simulations of product designs under a wide array of conditions, even before they hit the fabrication stage. By significantly reducing the need for physical prototypes, FEA expedites the design-to-market timeline, unlocking substantial savings in both capital and time resources.
-
Enhancing Prediction Accuracy
With FEA, businesses can expect to achieve an unparalleled level of prediction accuracy that traditional analysis methodologies often fall short of. FEA provides granular-level insights into critical parameters such as stress distribution, displacement, and strain, thereby enabling the production of high-fidelity, reliable products.
-
Stimulating Design Innovation
FEA serves as a catalyst for innovation, empowering businesses to venture beyond conventional design solutions with the aid of advanced FEA solutions. By facilitating a comprehensive understanding of product behavior under different scenarios, FEA fosters a problem-solving mindset, paving the way for market-disrupting products and a distinct competitive advantage.
-
Mitigating Operational Risk
FEA's predictive capabilities extend to identifying potential failure zones, thereby enabling businesses to take proactive measures to address product performance issues under extreme conditions. By ensuring product reliability and safety compliance, FEA plays a vital role in risk mitigation and brand reputation management.
-
Advocating Sustainability
FEA's contribution to sustainable practices is noteworthy. By optimizing material usage and minimizing waste, FEA enables businesses to design, analyze, and validate resource-efficient products. This aligns with the global shift towards sustainability and positions businesses favorably in an increasingly eco-conscious marketplace.
-
Enhancing Cost Effectiveness
FEA's ability to detect design imperfections early in the design process results in fewer iterations and reworks, translating into substantial cost savings. Additionally, its contribution to material optimization prevents unnecessary expenditure on surplus materials, thereby driving overall cost efficiency.
In Conclusion
Finite element analysis stands as a testament to the relentless pursuit of precision and excellence within the engineering discipline. Its proven capabilities have revolutionized the way we approach complex design and optimization challenges, making it an indispensable asset in the engineering toolkit. As FEA technology advances, it has the potential to open up even more opportunities and push the limits of engineering performance and creativity.
Partnering with a finite element simulation company can further amplify these benefits, offering specialized expertise and top-tier digital resources to tackle even the most daunting engineering challenges. The continuous advancements in processing power and algorithmic performance are driving FEA into uncharted application areas, broadening its impact across various sectors.
With finite element analysis, we enhance our capabilities for continuous improvement in various technical domains. The infinite potential of FEA, along with its constant evolution, expands our ability to design and implement projects that are currently speculative. This potent tool ensures a future filled with remarkable advancements in technology.
Contact UsAvail best-in-class services at affordable rates
Our Customers



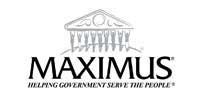

Key Differentiators
Case Studies
-
Flatworld Solutions provided customized CNC programming using MasterCAM
-
Flatworld Provided CFD Simulation Services to a Leading HVAC Products Manufacturer
-
Flatworld Solutions Offered Mechanical Instrument Drafting and Detailing Services to an Engineering Consultant
-
Flatworld Solutions Offered US Client with 2D to 3D Mechanical Legacy Drawing Conversion
-
Flatworld Solutions Provided Reverse Engineering of Machine Parts to a Client
Join the growth phase at Flatworld Solutions as a Partner
Service distributorship and Marketing partner roles are available in select countries. If you have a local sales team or are a person of influence in key areas of outsourcing, it's time to engage fruitfully to ensure long term financial benefits. Currently business partnerships are open for Photo Editing, Graphic Design, Desktop Publishing, 2D and 3D Animation, Video Editing, CAD Engineering Design and Virtual Walkthroughs.
Reach out to us for a quick direct response from decision makers at the Flatworld Solutions global team.
FAQs

USA
Flatworld Solutions
116 Village Blvd, Suite 200, Princeton, NJ 08540
PHILIPPINES
Aeon Towers, J.P. Laurel Avenue, Bajada, Davao 8000
KSS Building, Buhangin Road Cor Olive Street, Davao City 8000